Logistic services provider Soditra Logistic is expanding its existing warehouse in Nivelles (Belgium) to be able to centralize all warehousing activities for customer L’Oréal. Next to the existing robotized picking zone for medium and slow movers and the pallet warehouse, SAVOYE will install a new zone-to-zone picking system. The project comprises the delivery of flow racks, a box closing machine, weighing machines, conveyors and a WaCS to control the system. Furthermore, SAVOYE will realize a connection between the two zones by integrating an extra conveyor line for waste and excessive cardboard.
Moving without interruption
Belgian Soditra Logistic has been acting as 3PL supplier for L’Oréal for many years, with its first warehouse in Mollem (Asse), north of Brussels. In those days, L’Oréal still managed part of its logistic process themselves, in a Dutch site. Over time however, more and more work was outsourced to Soditra Logistic. The logistic specialist expanded their portfolio with Value Added Services, such as the assembly of point of sale displays, foil-shrinking products (hot & cold) after the conditioning and de-conditioning activities, all depending on the requirements of L’Oréal’s customers.
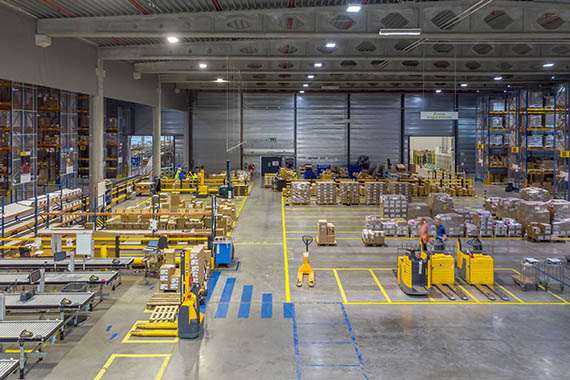
The goal of L’Oréal was to add more flexibility, reactivity, and above all more synergy to their process. In the end, this is why they decided to outsource all activities for the Benelux to their loyal partner Soditra Logistic.
This development kick-started an internal reorganization in which the activities for other customers will move to Mollem and the logistics services for L’Oréal will be centralized under one roof in Nivelles. This location will be expanded from 16,000m2 to 30,000m2, with a complete refurbishment.
Rearranging the logistic puzzle
The activities in Nivelles can be divided into three parts:
- Complete pallets in and out
- Standard orderpicking. The orderpicker collects products and builds up the complete pallet/order.
- Detail picking; a box/package is built up with different items. At first, this was done with picking trolleys. In 2018, a new technology was implemented: AMR robots and mobile shelvings in combination with four picking stations.
The organization above was mainly determined by the rotation classes of the products; the fast movers and the slow movers, 20%-80% of the SKU’s in stock and 80%-20% of the flow of goods.
Now that all the L’Oréal work had to be gathered under one roof, the next important question had to be answered: “What is the best mix of systems and equipment to get everything done in the best possible way?”
The advantages and disadvantages of both goods-to-man and man-to-goods solutions were carefully analysed, keeping the rotation classes as a the starting base. Man-to-goods systems simplify the re-stocking process, but they provide less output. With goods-to-man solutions, it is exactly the other way around. A study was conducted to design the best solution.
The connected zones
One of the conclusions from the report was that merging all product classes within just one system would not work. The decision was made to keep the different picking zones. Nevertheless, somehow the orders with products from the two different zones had to be brought together. Besides, ROI and productivity had to be improved with the new set-up. SAVOYE developed a solution in which the boxes travel through both zones via a conveyor system in order for combined orders to end up in same box. With this solution, Soditra Logistic not only realizes a productive output, but they will also reduce their carbon footprint and thereby adhere to the standards of L’Oréal. Basically, Soditra Logistic uses four different types of boxes that can all be closed by the same machine.
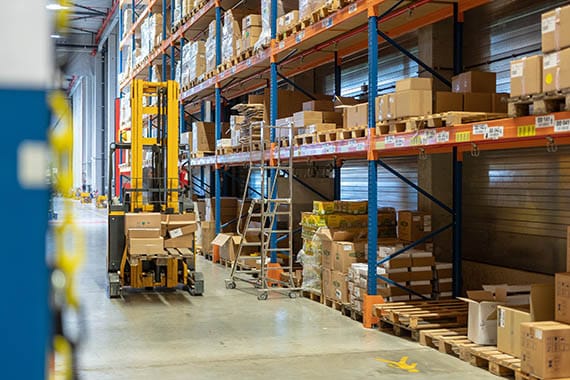
After the zone with robots, the conveyor transports the boxes to the zone-to-zone picking area, where flow racks (goods are fed in through the back) and an amount of picking stations will be used. The open boxes are transported in front of them. RF technology is used to indicate the quantities to be placed in the box. Finally, the boxes arrive at one of the eight exit lanes to be prepared for shipment.
Remarkable and particularly efficient is the solution to remove the empty packaging from the picking stations. SAVOYE integrates an extra conveyor belt next to the main line, which will transport all waste material directly to a shredder.
Jean-Luc Waetermans, Business Development Director at Soditra Logistic explains: “It has been quite a puzzle to simultaneously expand and refurbish the premises in Nivelles. We had just one year to complete the entire process, during which it was no option to pause or stop the daily activities. SAVOYE helped us to come up with and to design this integrated solution. The cooperation is going according to plan and we expect to be fully operational in July. Including a more productive and efficient process in the warehouse.”